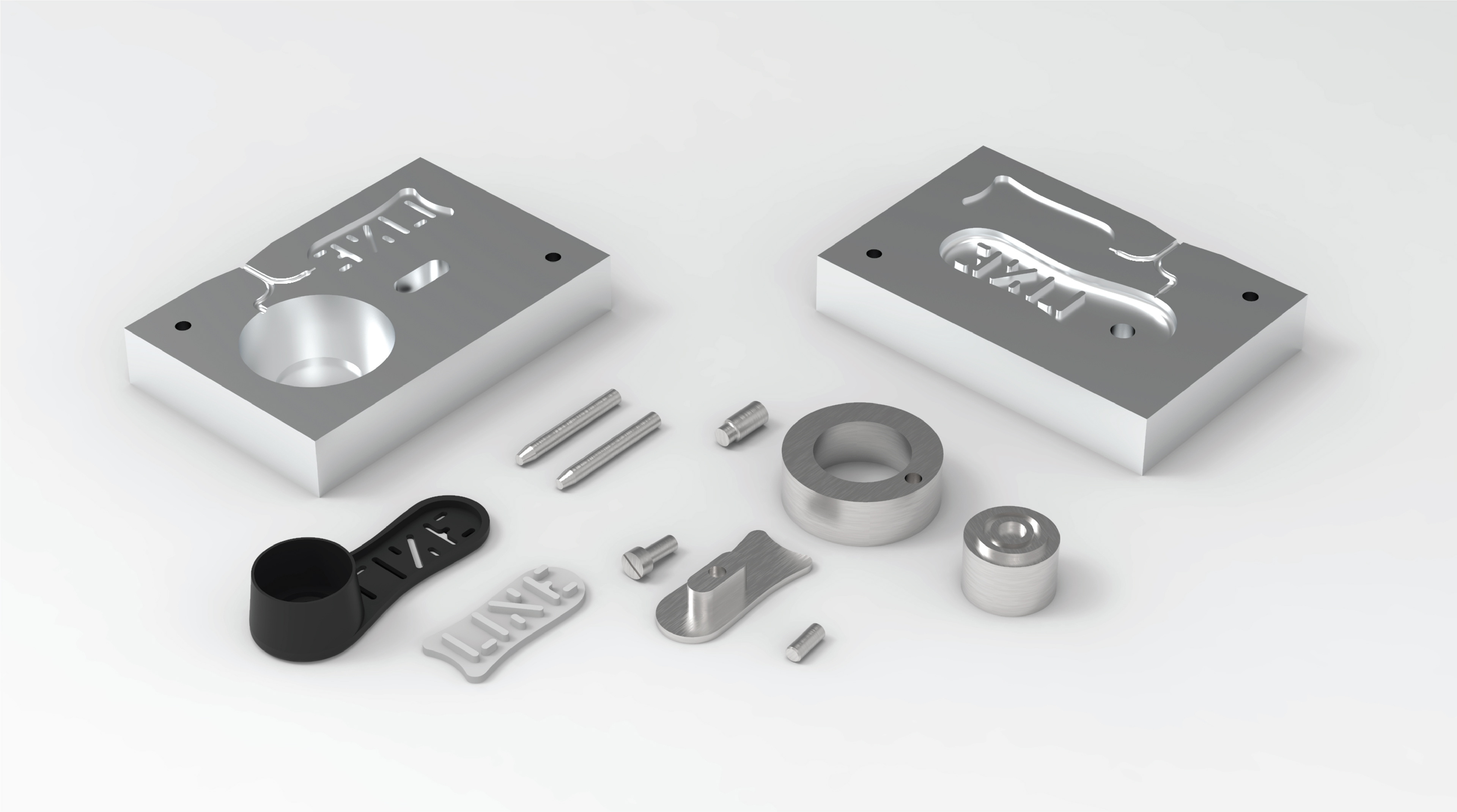
Project Outcome: In this 12 week project, I designed a universal ski pole widget and its prototyping mould, which was then selected for the following mould manufacture group project. This project has allowed me to gain skills in mould design for both commercial and prototyping manufacture levels. Exploring material properties in Granta provided me with useful information to help aid material and design decisions.
I chose Line Skis as the brand to promote within my widget due to their distictive logo. As the product was an adaptation of Line’s Grab Tab, I quickly arrived at a design solution which would work on freestlye ski pole grips from a wide range of brands.
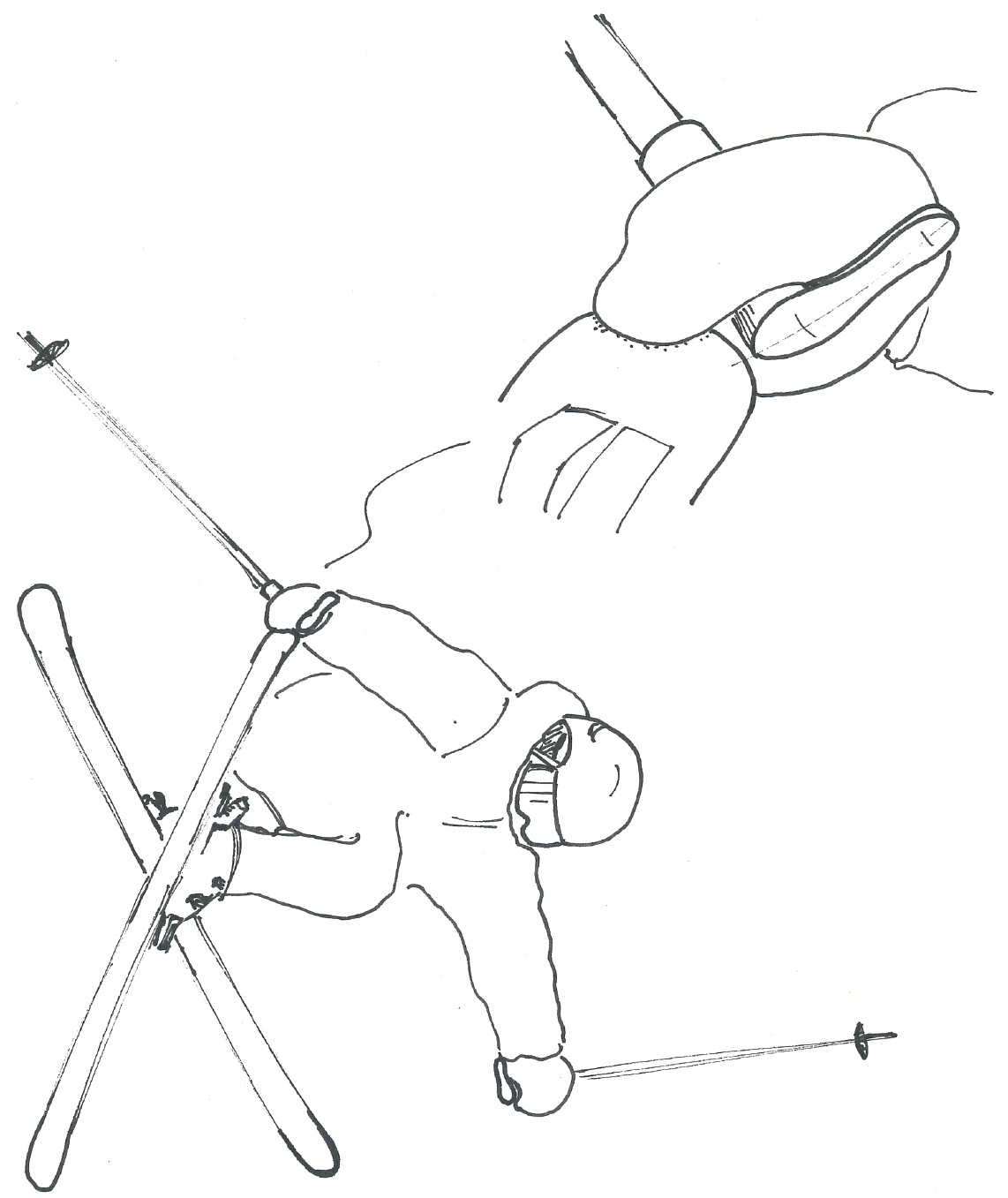
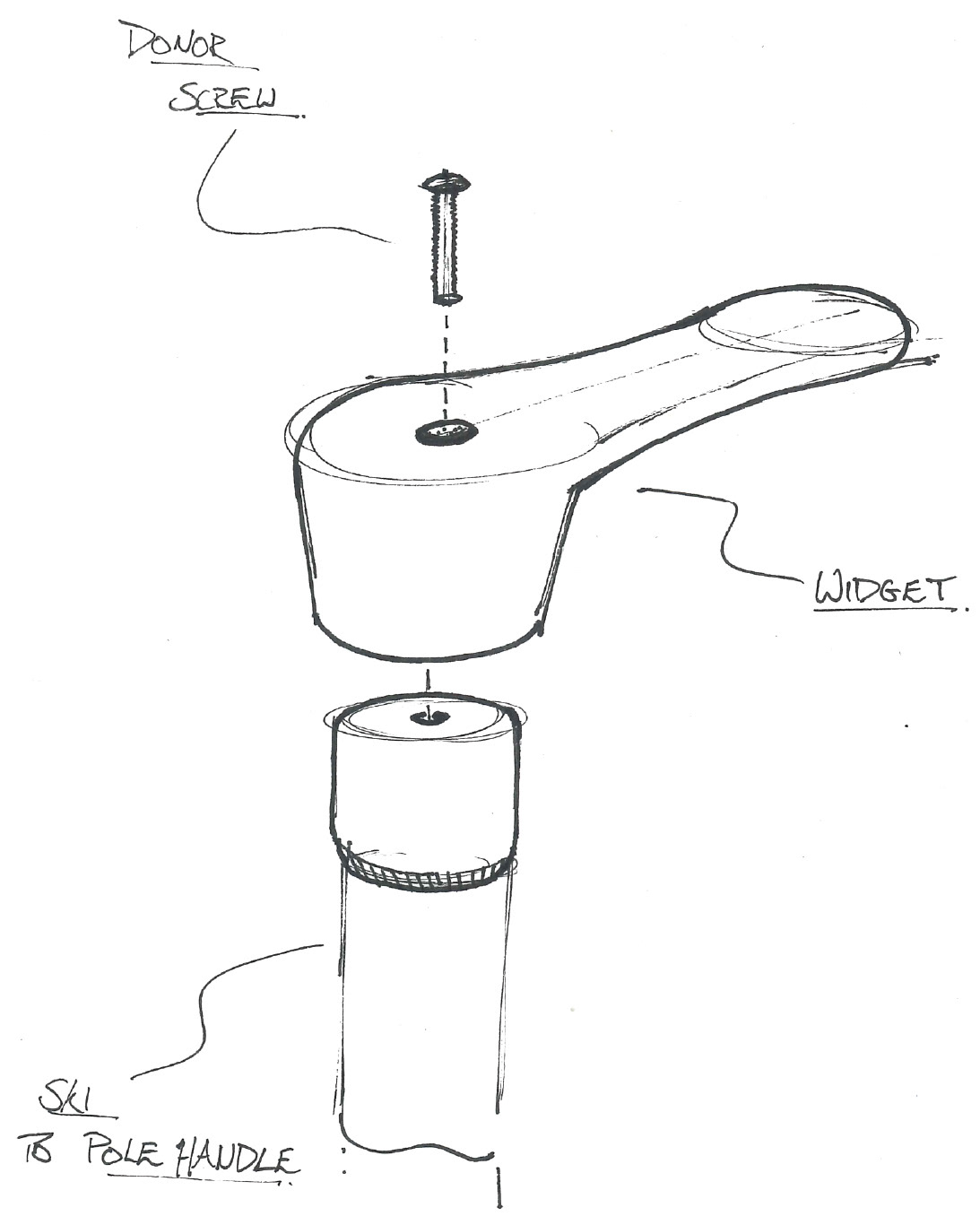
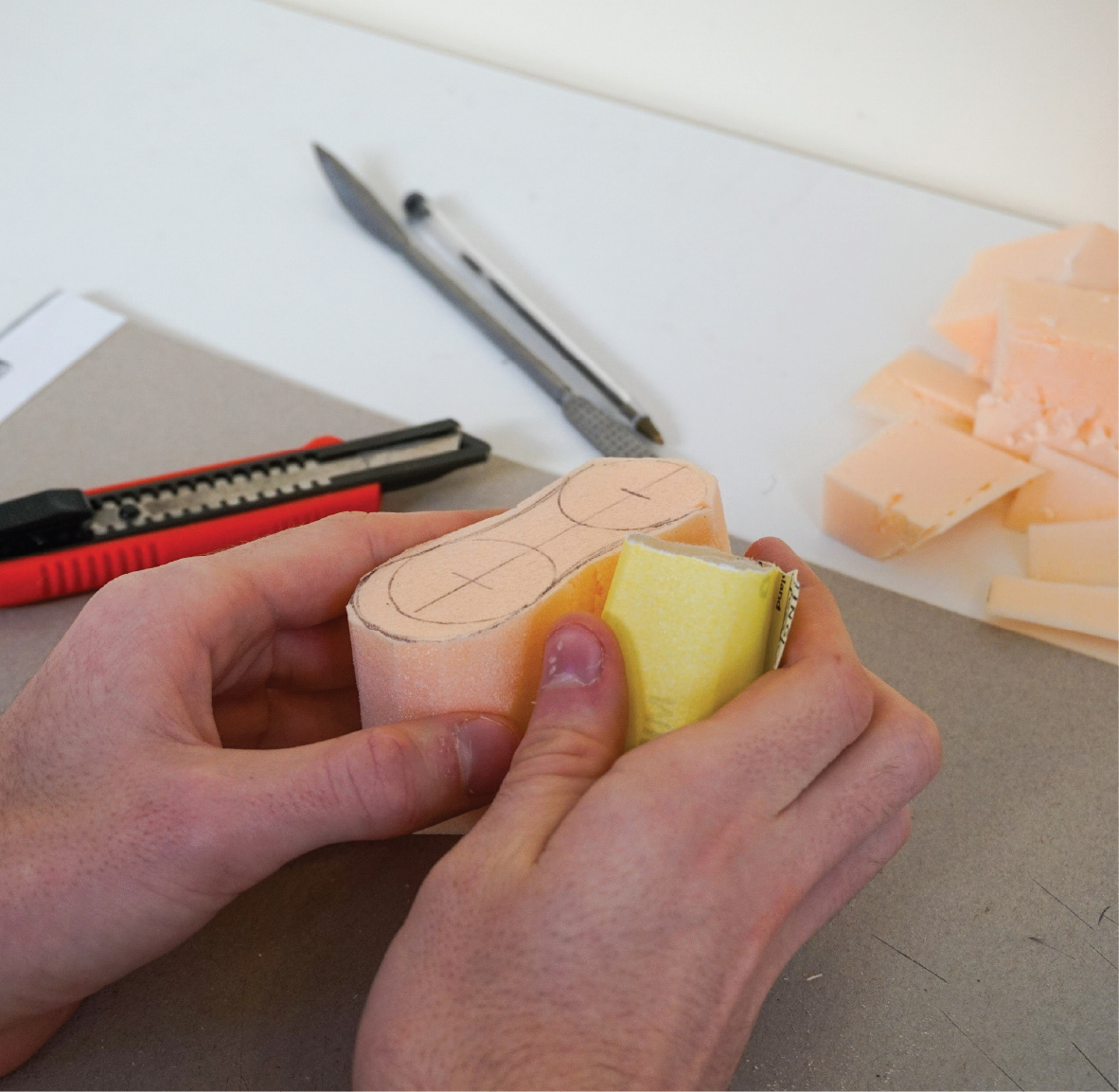
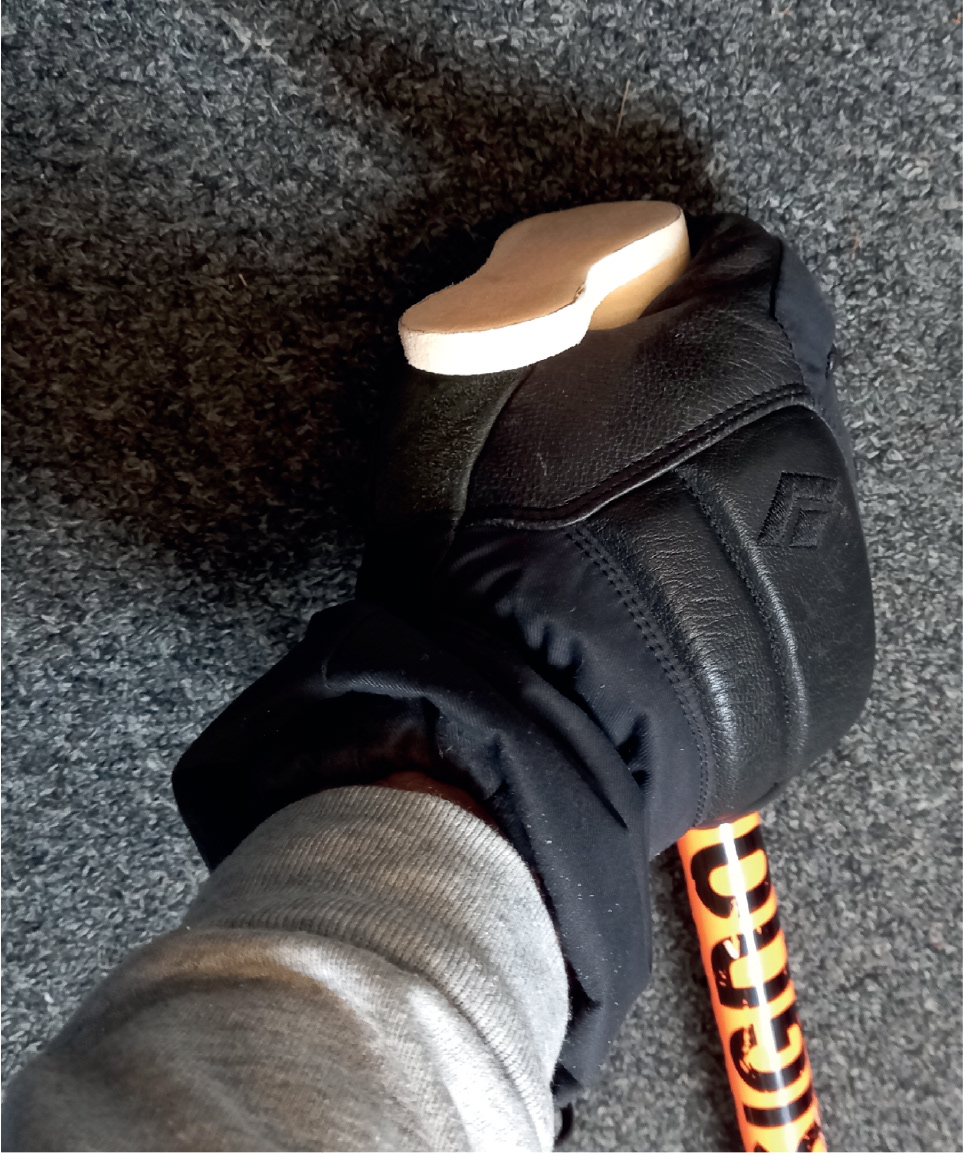
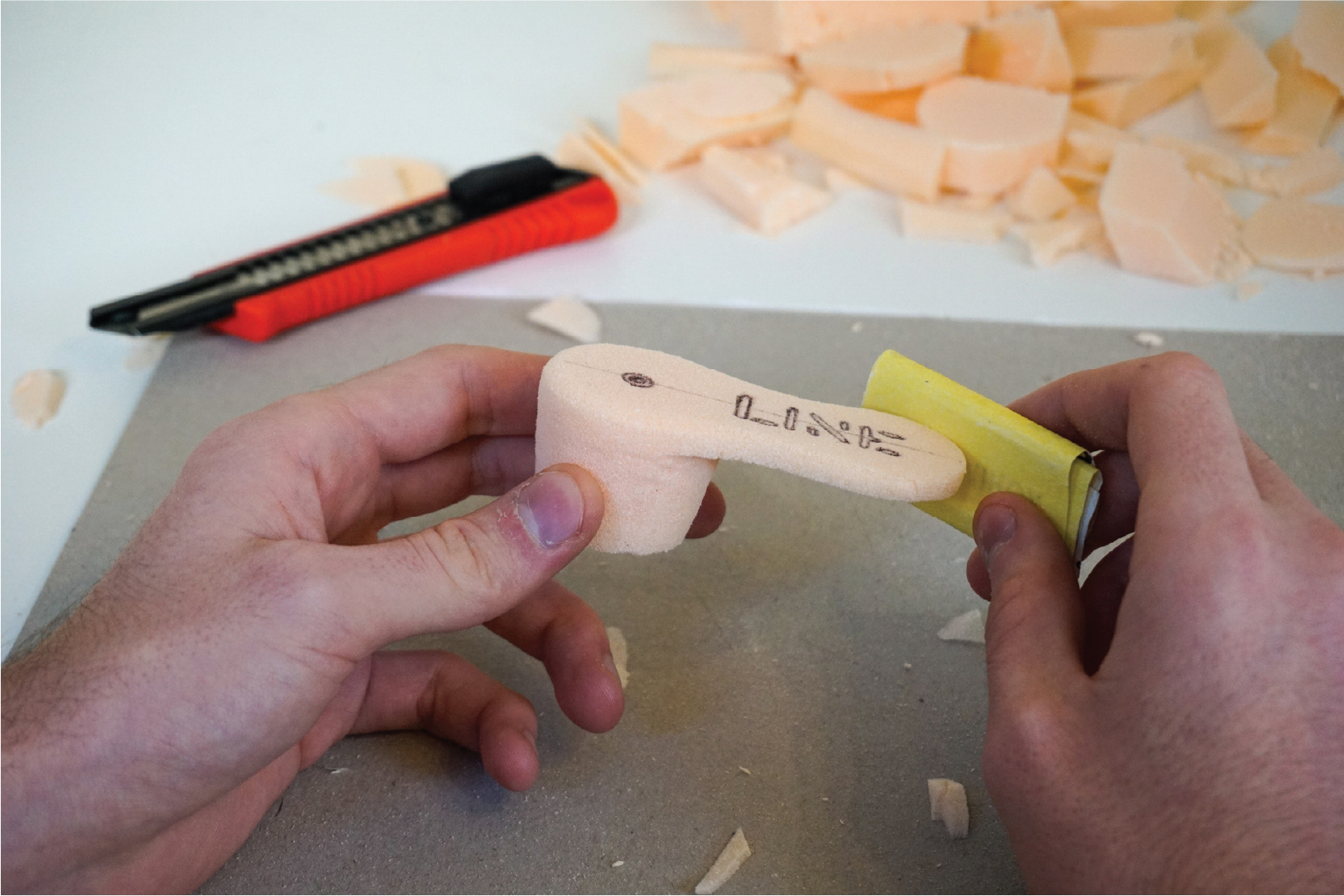
Rapid Foam modelling was carried out to understand the form and aid CAD development.
Using Solidworks Plastics, I was able to simulate the sink marks, ease of fill and the fill time of the mould. These factors helped me improve the mould design.
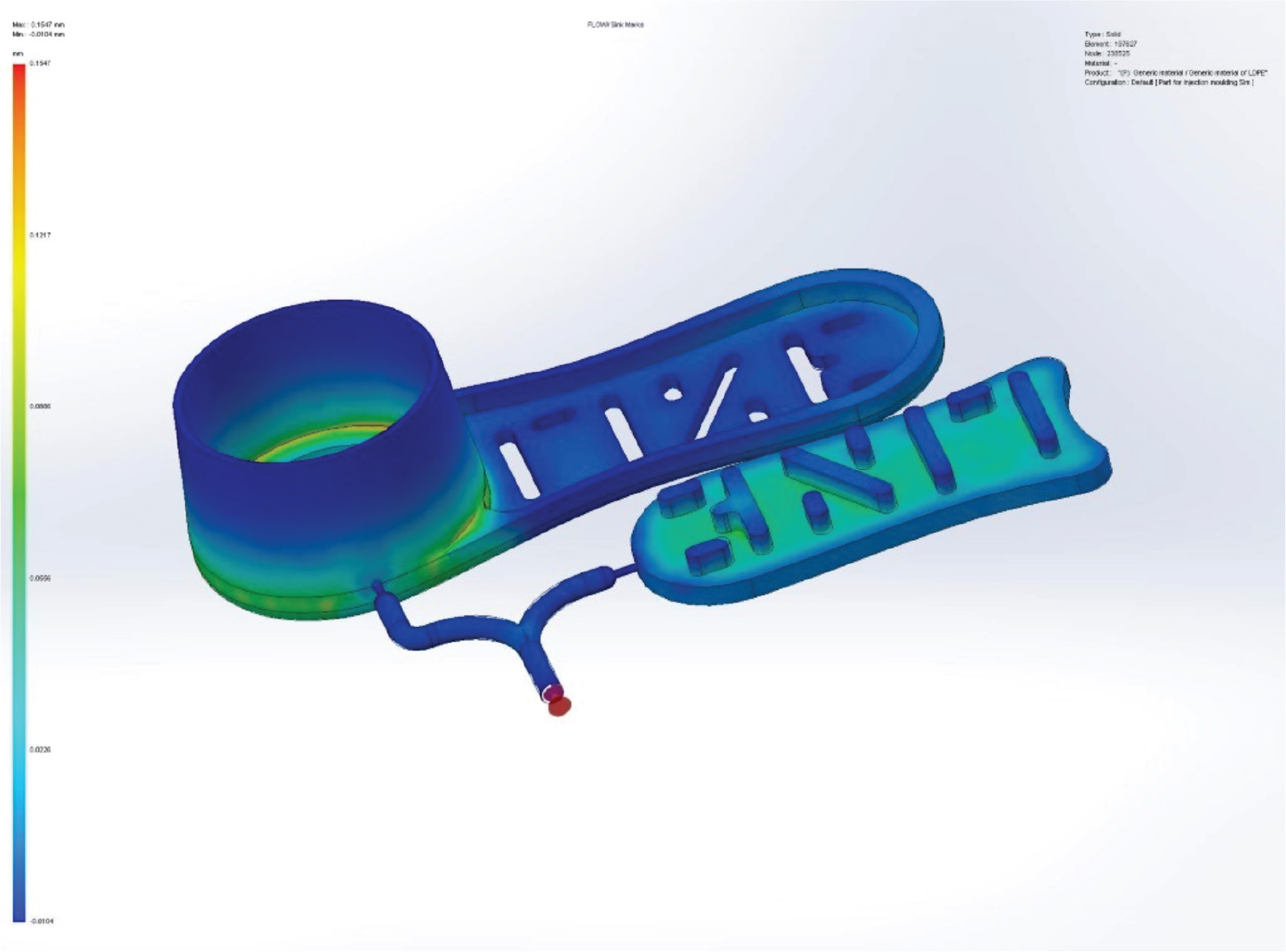
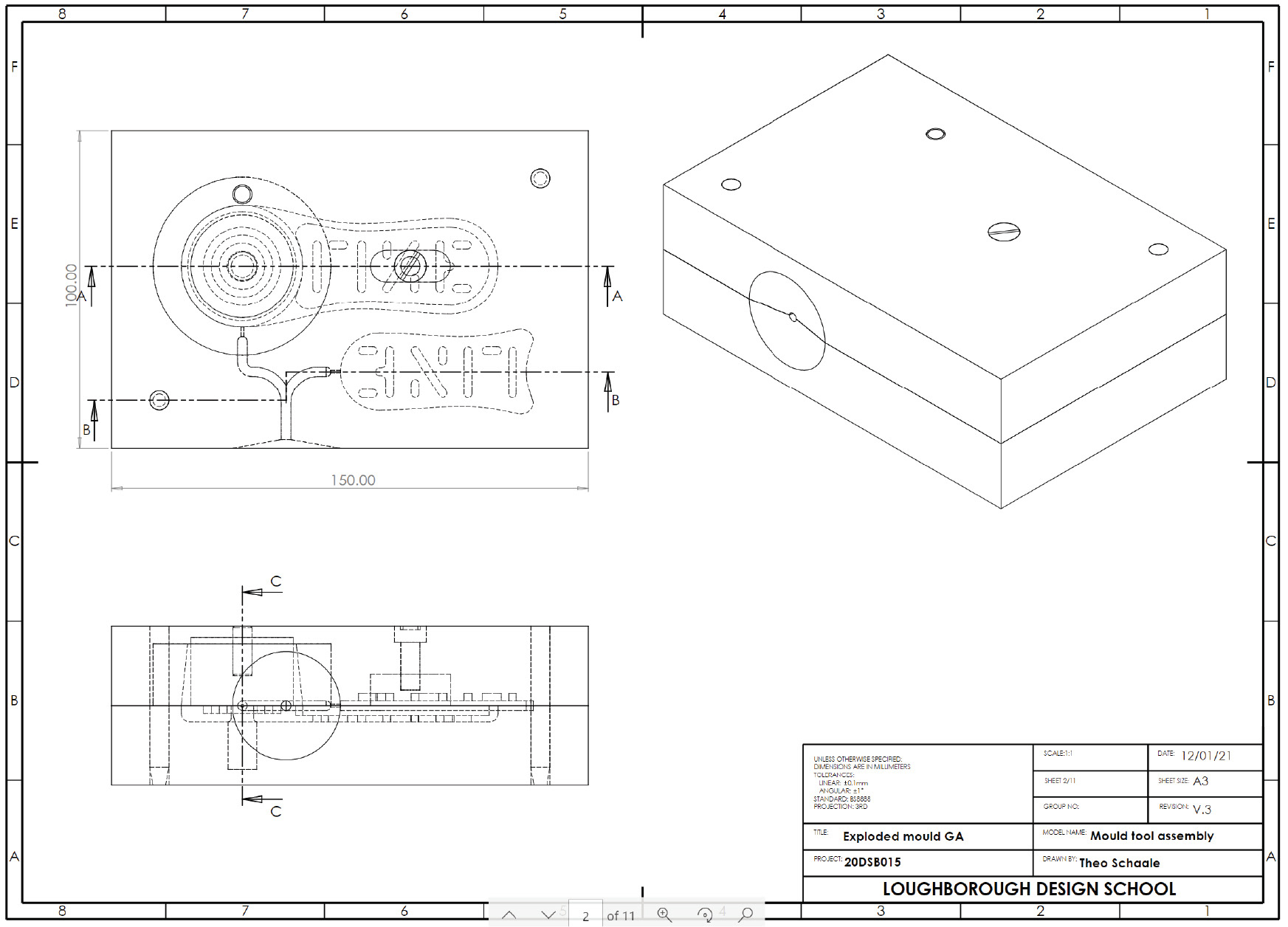
With the widget simulation showing appropriate feasability, I produced engineering drawings for manufacture.
The images on the right illustrate how the two parts of the widget fit. The exploded mould shows how the inserts fit within the mould and how the two parts of the Grab Tab are fitted together to promote the Line brand.
The aluminium mould halves are designed to be CNC milled where the majority of the stainless steel inserts are to be cut to size on a lathe. I applied tolerances to the BS8888 standard to ensure industry quality throughout the design.
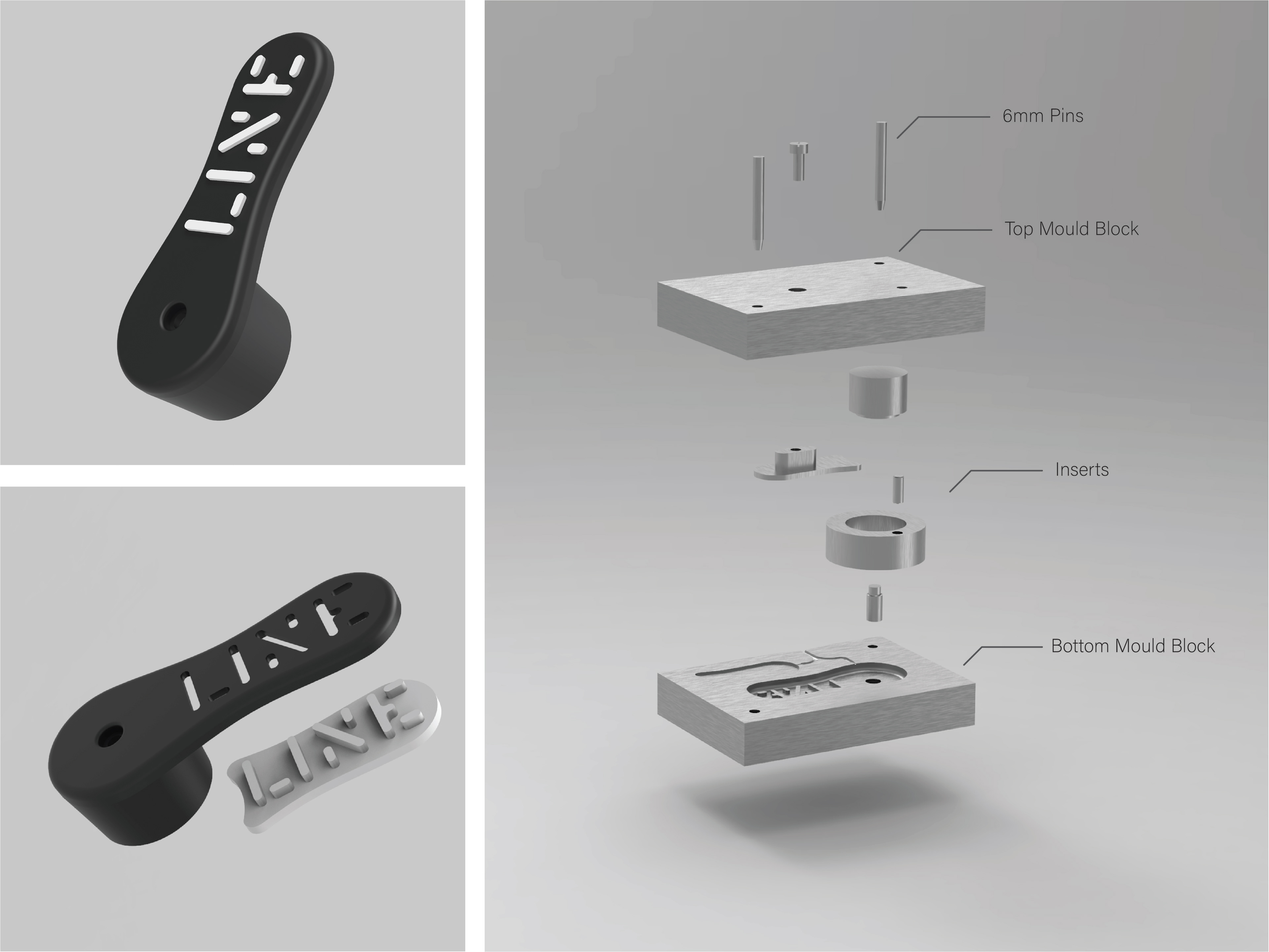
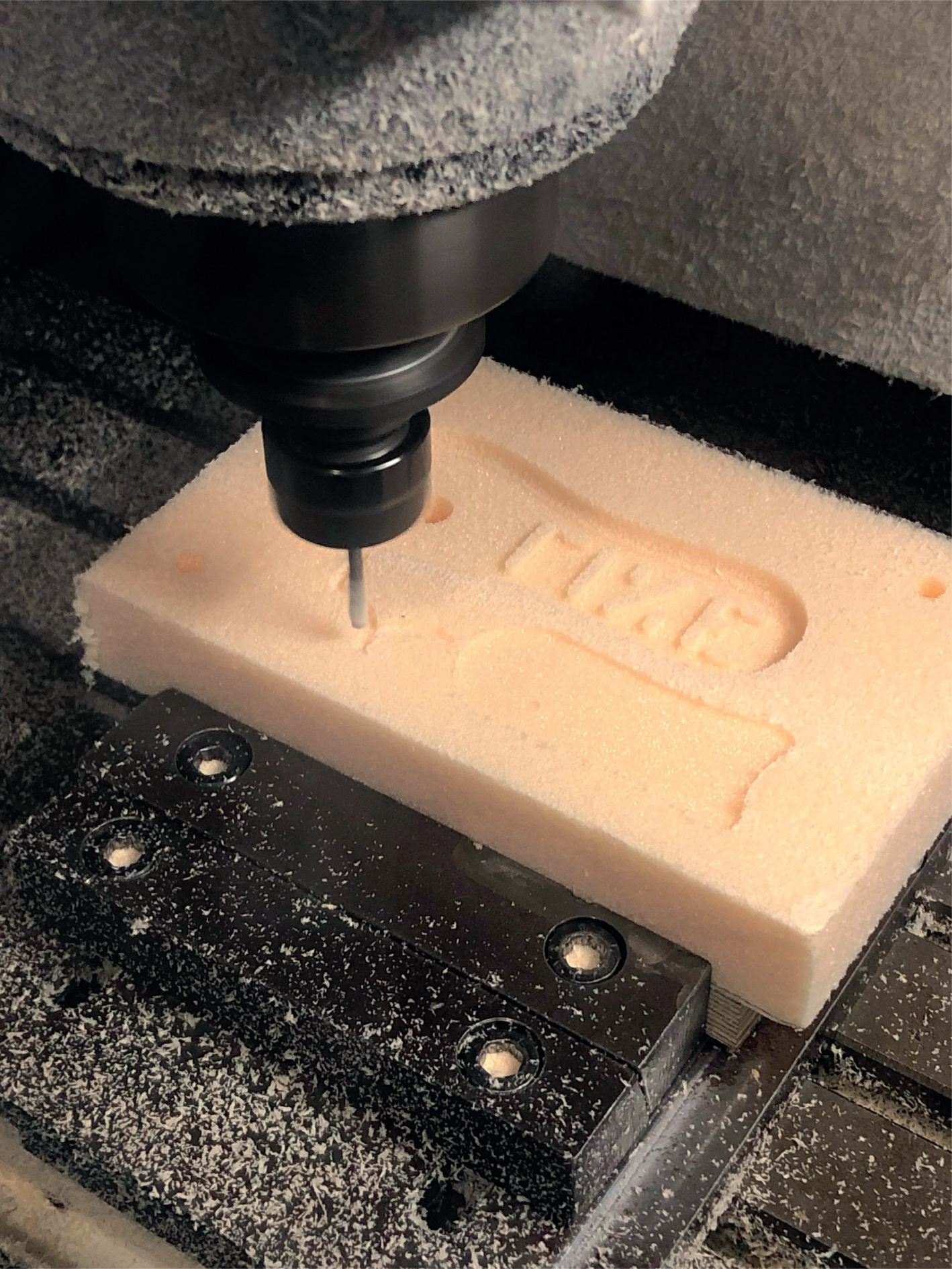
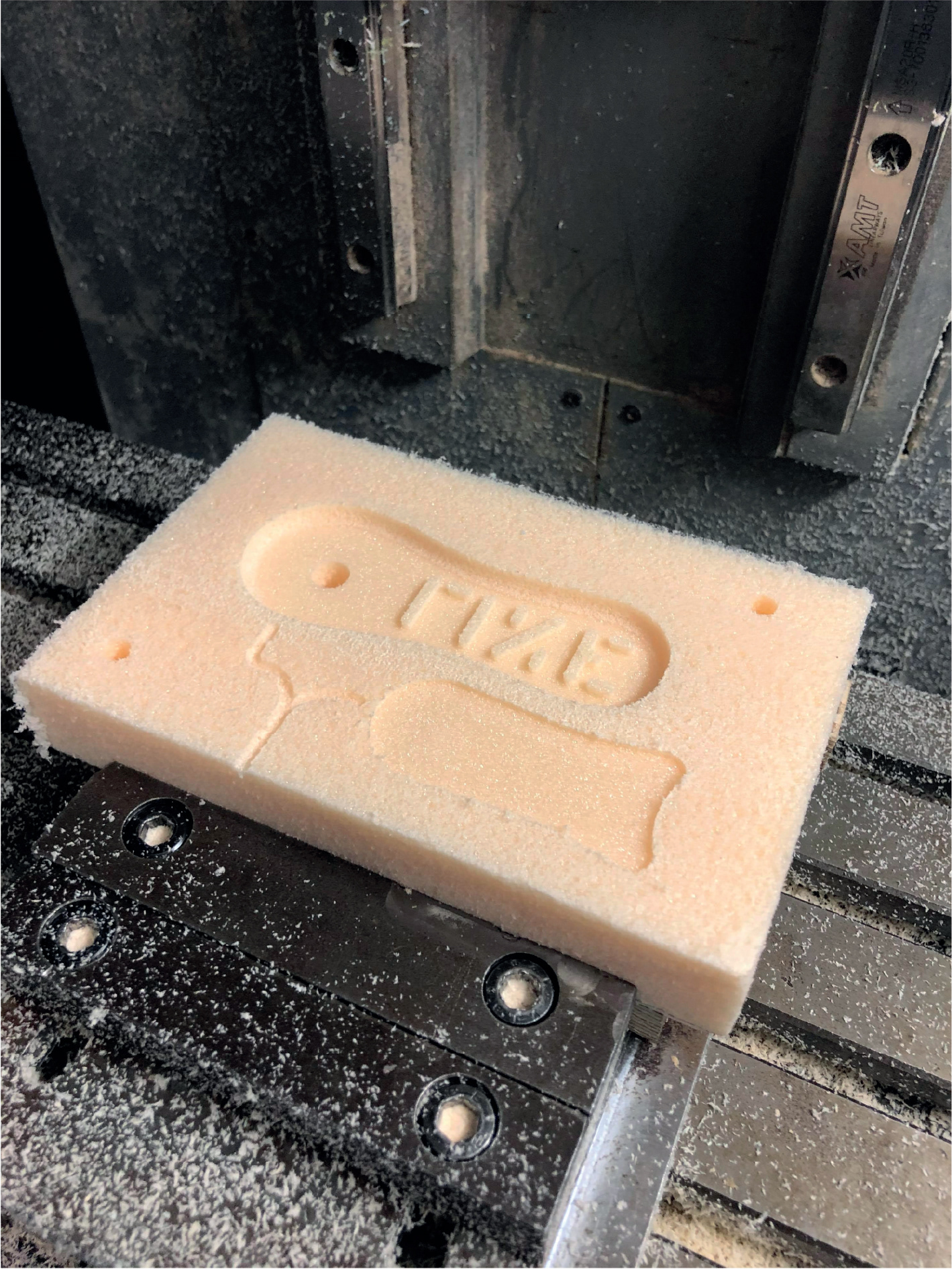
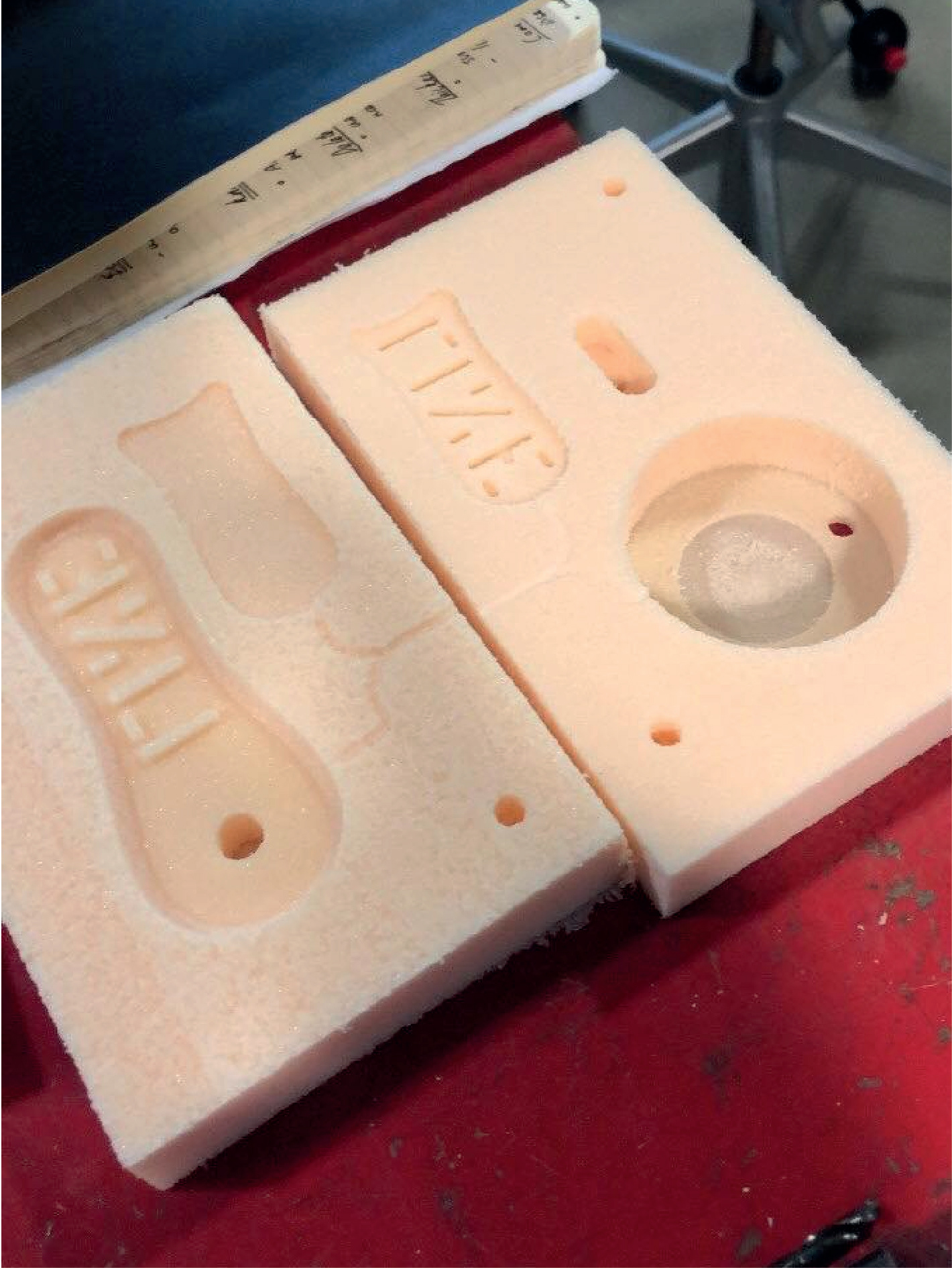
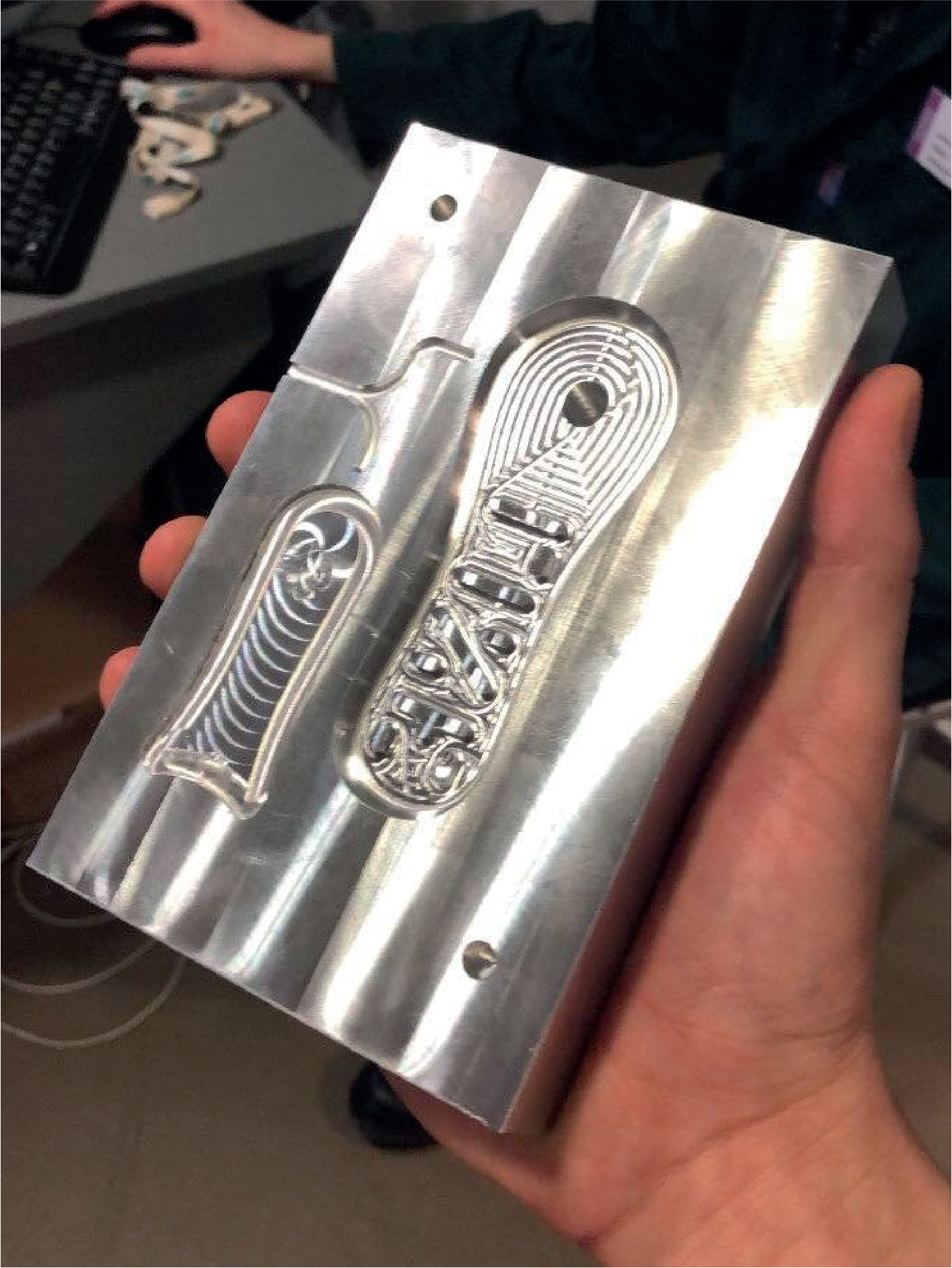
Using CNC Simulation within Solidworks enabled me to program the cutting paths and depths within the mould. The mould was first cut in foam to help identify errors.
an aluminium block was faced off and cut to the intended shape to make up the top mould. Covid measures unfortunately stopped workshop progress.
As part of our group project submission, we were required to produce an A0 poster which would detail our chosen material as well as our understanding of how we mass produce 3 million units in 13 weeks.
Further research was carried out to find out which material was best suited to our product. We had to consider the durability when it is used in its extreme enviroment and how it would perform under impacts from the user.
Using an Excel spreadsheet and information derived from Solidworks plastics, we calculated the cycle times for each of the 6 sections of injection moulding and how many moulds would be needed to meet demands.
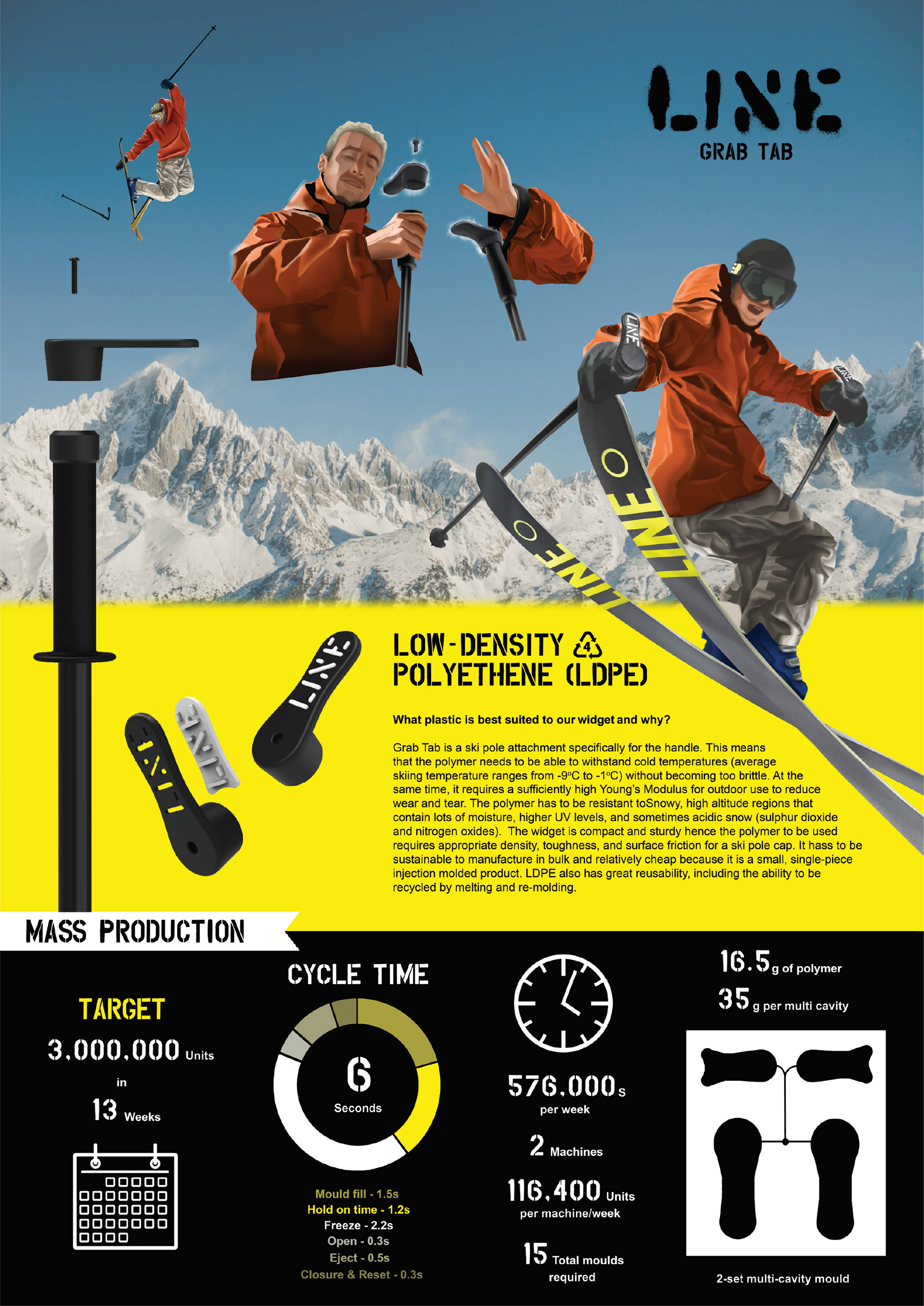